Materials Science – From Atoms to Advanced Manufacturing
Materials science addresses how substances behave, how they can be manipulated, and how new materials may be devised for specific needs. This field integrates physics, chemistry, engineering, and more to examine the connection between a material’s microscopic structure and its observable traits. Every product—from microchips to skyscraper steel—relies on fundamental insights about material composition and performance. Below is a detailed guide covering key topics ranging from atomic structure to manufacturing processes and future developments.
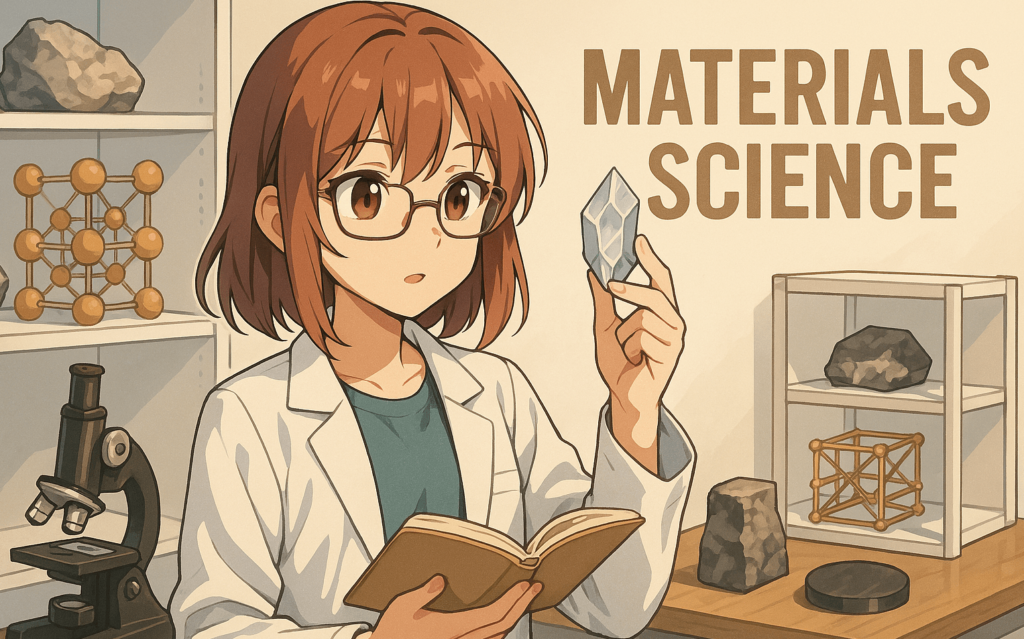
1. Introduction
Materials science seeks to understand, design, and improve substances for various industries. Historical progress often followed breakthroughs in materials: the Bronze Age emerged with metal alloys, modern electronics rely on semiconductors, and current research attempts to refine or develop materials at the nanoscale. Specialists study how atomic arrangements and bond types affect mechanical, thermal, electrical, and chemical properties. By modifying compositions or processing methods, they can craft materials that meet requirements in aerospace, medicine, energy, and computing.
2. Atomic and Molecular Structure
2.1. Atoms and Bonding
The structure of a material stems from its atoms and the bonds that hold them together. Metallic bonding involves a “sea” of electrons shared among positive ion cores, giving rise to electrical conductivity and ductility. Ionic compounds form when electrons transfer between species, generating a lattice of cations and anions (e.g., sodium chloride). Covalent networks (like diamond or silicon) feature shared electron pairs that yield strong directional bonds. Many materials exhibit combinations of these bond types, influencing stiffness, melting temperature, or brittleness.
2.2. Crystalline vs. Amorphous Solids
Crystals arrange atoms or ions in regular, repeating patterns (e.g., face-centered cubic, body-centered cubic). Metals frequently crystallize with high symmetry, enabling slip systems that permit plastic deformation. Ceramics adopt varied structures and can have complex oxygen-metal frameworks. Polymers may exhibit partially crystalline regions and amorphous domains. Amorphous solids, such as glass, have disordered atomic networks lacking a long-range pattern, which impacts transparency and brittleness. Understanding these structural motifs helps interpret how materials behave under stress or temperature changes.
2.3. Defects and Microstructure
Real materials contain imperfections. Point defects include vacancies (missing atoms) or interstitial atoms lodged between lattice sites. Linear defects (dislocations) are crucial in metals, as they mediate plastic deformation. Planar defects, such as grain boundaries between differently oriented crystals, can improve or reduce properties depending on context. For instance, adding a small fraction of dislocations to a metal can make it stronger, but too many might lead to brittleness. Controlling microstructure—grain sizes, phases, and defect densities—forms a core strategy for tailoring performance.
3. Material Classes
3.1. Metals and Alloys
Metals typically have high thermal and electrical conductivity, along with ductility and luster. Iron, aluminum, copper, and their alloys remain foundational for modern infrastructure. Steel, an iron-carbon mixture, underpins construction, with variations like stainless steel (adding chromium and nickel) offering corrosion resistance. Lightweight metals (like aluminum, titanium) help in aerospace, while specialty alloys (nickel-based superalloys) operate at extreme temperatures in jet engines.
3.2. Ceramics and Glasses
Ceramics are mostly compounds of metals with oxygen, nitrogen, or carbon (e.g., alumina, silicon nitride). They exhibit strong bonds, high hardness, and resilience against heat or chemical attack but often lack ductility. Typical uses include pottery, tiles, cutting tools, and advanced components in electronics or turbines. Glass forms when certain melts solidify without crystallization, leading to an amorphous structure that grants transparency. Traditional soda-lime glass is common in windows and containers. Advanced glasses (borosilicate, fused silica) possess better thermal shock resistance or purity.
3.3. Polymers
Polymers are large molecules assembled from repeating subunits (monomers). Natural examples include cellulose, silk, and rubber; synthetic polymers encompass polyethylene, nylon, and polystyrene. The arrangement of polymer chains, branching, and crosslinks strongly influences elasticity, toughness, or thermal stability. Some (thermoplastics) melt upon heating, while others (thermosets) form permanent networks that resist reshaping. In consumer goods, packaging films, textiles, and automotive parts, polymeric materials often provide cost-effective solutions, although they can raise concerns about biodegradability or microplastic pollution.
3.4. Composites
Composites combine two or more distinct materials to leverage complementary advantages. A common example is fiberglass, where glass fibers reinforce a polymer matrix for improved strength-to-weight ratio. Carbon fiber composites excel in aerospace or sports equipment, providing stiffness with minimal mass. Concrete can be seen as a composite of cement paste and aggregate. These multi-phase systems allow fine-tuning of mechanical properties, corrosion resistance, or thermal behavior, making them appealing in advanced engineering.
3.5. Semiconductors
Semiconductors like silicon or gallium arsenide have intermediate electrical conduction, essential in electronic devices. By doping with specific impurities (phosphorus, boron, etc.), scientists can shift the electron or hole concentrations, forming p-type or n-type regions that yield diodes, transistors, and integrated circuits. Thin-film semiconductors also power solar cells, converting sunlight into electricity. Ongoing efforts aim to refine materials for faster computing, improved energy efficiency, and advanced sensors.
4. Material Properties
4.1. Mechanical Properties
- Strength: Ability to withstand stress without failure.
- Toughness: Capacity to absorb energy prior to fracturing.
- Hardness: Resistance to localized surface deformation or scratching.
- Ductility: Degree of plastic deformation possible before fracture.
- Elasticity: Reversible deformation under load.
Properties can differ widely based on composition and structure. For instance, a tempered steel might exhibit high tensile strength and toughness, while a ceramic can support large compressive forces yet crack under tensile loads.
4.2. Thermal Properties
Thermal conductivity affects how quickly heat moves through a substance, vital for electronics heat sinks or insulation materials. Thermal expansion describes how volume changes with temperature, impacting component tolerances (e.g., expansion joints in bridges). Melting points define processing windows, especially relevant for metals or polymers during manufacturing.
4.3. Electrical and Magnetic Properties
Conductivity can range from metals (silver, copper) at the high end to insulators (plastics, ceramics) at the low end. Semiconductors occupy a middle ground, enabling transistor operation. Superconductors conduct electricity without resistance below certain temperatures. Magnetic materials (ferromagnetic, ferrimagnetic) store data in computers or produce motor torque. Careful doping or heat treatments can modify conductivity or magnetic coercivity.
4.4. Optical Properties
Optical characteristics—reflectivity, transparency, refractive index—depend on electronic band structures or scattering. Transparent polymers find use as lightweight window replacements, while reflective metals coat mirrors. In photonics, controlling light propagation in waveguides or optical fibers hinges on doping levels and structure. Materials with carefully engineered band gaps can emit or absorb specific wavelengths, useful in lasers, LEDs, or solar cells.
5. Phase Diagrams and Microstructures
5.1. Phase Diagrams
Phase diagrams map the stable phases of a system under varying composition, temperature, or pressure. A binary phase diagram (like iron-carbon) shows how steel evolves from ferrite or austenite to eutectic structures. Ternary or multi-component diagrams tackle more intricate alloy or ceramic formulations. Engineers consult these charts to pinpoint heat treatments or compositions that yield desired microstructures. For example, controlling cooling rates can create fine grains or special phases that boost strength.
5.2. Phase Transformations
When temperature or composition shifts, materials may undergo transformations: from solid to liquid, from one crystal form to another, or precipitation of new phases within a matrix. Transformations can be diffusion-controlled (like pearlite formation in steel) or diffusionless (martensitic transformations). Some transformations, such as shape-memory alloys (NiTi), store a deformed shape and revert under heating. Precise management of these transformations leads to advanced properties or specialized functionalities.
6. Manufacturing and Processing
6.1. Metals Processing
- Casting: Molten metal poured into molds, creating complex shapes.
- Rolling and Forging: Deformation to refine grain structures and enhance strength.
- Heat Treatment: Annealing, quenching, or tempering modifies phases or relieves internal stresses.
- Powder Metallurgy: Compressing metal powders and sintering them to form near-net-shape products with minimal waste.
6.2. Ceramics and Glass Processing
Ceramics often form via powders shaped and sintered at high temperatures. Traditional approaches include slip casting or pressing. Advanced techniques add hot isostatic pressing or spark plasma sintering, achieving dense, near-porosity-free parts. Glass production typically involves melting silica-based mixtures, shaping by float processes or blowing, and controlled cooling to avoid internal stress.
6.3. Polymer Fabrication
Methods range from extrusion of continuous sheets or fibers to injection molding for intricate shapes. Thermoplastics can be remelted, but thermosets cure irreversibly. Compounding with additives (plasticizers, stabilizers, fillers) adjusts mechanical or thermal performance. 3D printing of polymers has gained popularity for rapid prototyping or low-volume manufacturing.
6.4. Additive Manufacturing
Additive manufacturing, commonly called 3D printing, builds objects layer by layer from digital designs. Polymers, metals, and ceramics can all be processed through various means (fused filament fabrication, selective laser melting, stereolithography). This approach enables internal features, lightweight lattices, and customization. Challenges include controlling residual stress, ensuring consistent microstructures, and verifying part quality. Nevertheless, it opens new frontiers in complex geometry and on-demand production.
7. Characterization Techniques
7.1. Microscopy
- Optical Microscopy: Observes microstructures or defects. Etching highlights grain boundaries in metals.
- Scanning Electron Microscopy (SEM): Bombards samples with electrons, generating high-resolution surface images. X-ray signals (EDS) reveal element distributions.
- Transmission Electron Microscopy (TEM): Electrons pass through ultrathin sections, exposing fine details like dislocations, precipitates, or atomic planes.
- Atomic Force Microscopy (AFM): A sharp tip scans surfaces to map topography at nanoscale.
7.2. Spectroscopy and Diffraction
- X-ray Diffraction (XRD): Determines crystal structures and identifies phases. Peak positions and intensities yield lattice parameters.
- Raman and Infrared Spectroscopy: Probes vibrational modes, verifying compositions in ceramics or polymers.
- Energy-Dispersive X-ray Spectroscopy (EDS): Coupled to electron microscopes for elemental analysis.
7.3. Mechanical Testing
Mechanical tests establish stress-strain curves, fracture toughness, or hardness. Tensile tests measure yield strength and ductility. Impact tests gauge how materials behave under sudden loads. Fatigue tests reveal how repeated cyclic stress leads to eventual failure. Hardness tests (Rockwell, Vickers) evaluate resistance to indentation. These methods guide material selection in load-bearing applications.
7.4. Thermal and Electrical Measurement
Differential scanning calorimetry (DSC) locates phase transitions, melting points, or glass transitions. Thermogravimetric analysis (TGA) tracks mass changes upon heating. Electrical conductivity or resistivity tests verify doping effectiveness or confirm conduction mechanisms (metallic, semiconducting, or insulating).
8. Nanotechnology and Advanced Materials
8.1. Nanomaterials
Nanomaterials have at least one dimension under 100 nm. Quantum dots, carbon nanotubes, and graphene exemplify structures where quantum confinement or large surface-to-volume ratios yield novel properties. Graphene’s high conductivity and strength have sparked interest in flexible electronics or composites. Nanoparticles can reinforce polymers, enhance catalysis, or deliver drugs in medical contexts. However, concerns exist about toxicity, safe handling, and environmental fate, prompting research on responsible development.
8.2. Smart Materials
Smart or responsive materials adapt to external stimuli like temperature, pH, moisture, or stress. Shape memory alloys revert to a predetermined shape when heated, making them useful in actuators or stents. Piezoelectric ceramics produce electric voltage under mechanical load, aiding sensors and transducers. Electrochromic coatings change optical properties upon voltage, enabling dimmable windows. These materials advance technologies such as adaptive architecture or wearable devices.
8.3. Biomaterials
Biomaterials are engineered to interface with living tissue. They must be biocompatible, avoiding immune responses or toxicity. Polymers for sutures or scaffolds degrade at controlled rates. Titanium alloys or ceramics can serve as implants (e.g., hip replacements) with surfaces designed to promote bone growth. Tissue engineering research explores how to cultivate cells on artificial matrices, potentially regenerating organs or tissues for transplantation.
9. Sustainability and Recycling
Many organizations emphasize recycling or reusing materials to limit waste and conserve resources. Aluminum and steel recycling save large amounts of energy compared to primary production. Advances in polymer recycling face complications due to contamination or additive differences. Novel biodegradable polymers aim to reduce plastic pollution, though they must still match mechanical demands. Life cycle analysis (LCA) helps gauge the total environmental impact of material extraction, manufacturing, usage, and disposal.
10. Future Directions
Materials science continues to evolve in pursuit of improved performance, functionality, and ecological responsibility:
- Quantum Materials: Exploiting topological insulators or superconductors for advanced electronics and computing.
- Ultra-High-Temperature Ceramics: Safeguarding hypersonic vehicles or next-generation turbines.
- Energy Storage: Developing stable, high-capacity batteries (solid-state electrolytes, novel cathodes) to support renewable energy grids and electric vehicles.
- Flexible Electronics: Printable electronics and thin-film transistors open prospects for wearable sensors or roll-up displays.
- Bioinspired Materials: Mimicking biological processes to generate stronger, lighter structures or self-healing surfaces.
Cross-disciplinary research—combining computational modeling, data analytics, and experimental methods—stands poised to accelerate breakthroughs. Researchers also focus on scaling up lab innovations while adhering to regulations and cost constraints.
11. Wrapping It Up
Materials science underpins many technological achievements, from the alloys used in aircraft to the polymers in medical implants. By correlating atomic structures and manufacturing parameters with real-world performance, specialists devise substances that meet evolving needs in electronics, healthcare, transportation, and beyond. Ongoing advances in nanotechnology, additive manufacturing, and environmentally minded design promise to reshape how we create and use materials. As the global community tackles energy, sustainability, and healthcare challenges, materials remain central in forging practical solutions that align with safety and efficiency.