Chemical Safety – From Hazard Labels to Waste Management
Chemical safety aims to protect people, facilities, and the broader environment from harmful effects of chemicals. It covers identifying hazards, controlling exposure, and responding if accidents occur. This text presents an extensive look at chemical safety, addressing legislation, labeling, storage, personal protective equipment, disposal, and more. Following these guidelines helps reduce risks in laboratories, industries, schools, and anywhere chemicals are handled or stored.
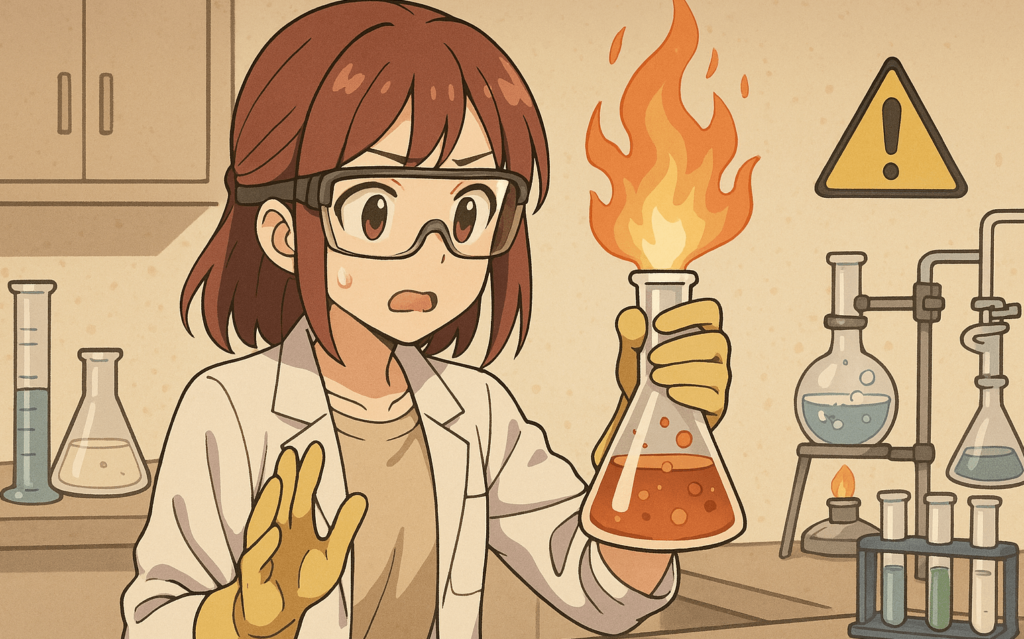
1. Importance and Foundation
No matter if one works in a research lab, industrial site, or small workshop, unsafe chemical practices can lead to fires, explosions, toxic exposures, and injuries. Over the past century, high-profile accidents spurred regulations and taught lessons regarding how to label, transport, or dispose of hazardous materials. Governments introduced rules, such as the Occupational Safety and Health Administration (OSHA) requirements in the United States or the Globally Harmonized System (GHS) for hazard communication, to standardize the approach to chemical safety.
These norms outline how to classify chemicals by their properties, how to communicate threats through labels and safety data sheets, and how to mitigate hazards through procedures and protective equipment. Employers also have a moral responsibility to ensure their staff know about chemical properties, safe handling, emergency procedures, and control measures. Universities and research centers typically maintain strict policies and training programs. Meanwhile, in a home or hobby environment, smaller volumes of chemicals still warrant caution. By following best practices, chemical interactions become safer and more predictable.
2. Hazard Communication and Classification
2.1. Globally Harmonized System (GHS)
The GHS standardizes how to categorize chemicals by physical, health, and environmental hazards. It uses signal words (like “Danger” or “Warning”), hazard statements (e.g., “Highly flammable liquid and vapor”), precautionary statements (e.g., “Keep away from heat/sparks/open flames”), and pictograms (like flame, exclamation mark, corrosive, etc.). These symbols and statements ensure workers, transporters, and the public grasp the nature of a product.
Countries may adapt GHS into their local regulations. For instance, the European Union uses the Classification, Labeling and Packaging (CLP) Regulation, while the United States uses Hazard Communication Standard (HCS). Regardless of region, the aim remains consistent: to label containers with clear, consistent warnings about chemical content and potential risks. Employers and suppliers must train workers to interpret labels, promoting awareness even for those who are new or do not speak the local language fluently.
2.2. Safety Data Sheets (SDS)
Formerly known as Material Safety Data Sheets (MSDS), these documents describe chemical properties, dangers, handling guidelines, and first-aid steps. An SDS typically follows a standardized format:
- Identification: Chemical name, recommended uses, supplier details.
- Hazards: Classification, label elements, potential health effects.
- Composition: Ingredients, concentration ranges.
- First-Aid Measures: Symptoms, immediate steps for inhalation, ingestion, or skin contact.
- Fire-Fighting Measures: Suitable extinguishing media, hazards from combustion.
- Accidental Release: Procedures for containment and cleanup.
- Handling and Storage: Precautions, safe conditions to prevent unintended reactions.
- Exposure Controls/PPE: Permissible exposure limits, recommended gear.
- Physical/Chemical Properties: Boiling point, density, pH, flammability.
- Stability/Reactivity: Conditions to avoid, incompatible materials.
- Toxicological Information: Routes of exposure, acute/chronic effects, toxicity data.
- Ecological Info: Potential harm to water bodies, persistence, bioaccumulation.
- Disposal: Methods to discard safely.
- Transport: UN numbers, packing group, hazard class.
- Regulatory Details: Local or global references.
- Other Information: Revision history, disclaimers.
Workers must have easy SDS access for each chemical in the facility. Reading an SDS in advance clarifies how to handle a substance and respond to an emergency.
3. Labeling Requirements
3.1. Primary vs. Secondary Containers
All chemical containers need labels indicating contents and hazards. Primary containers arrive from manufacturers with official GHS labels, including hazard pictograms, signal words, and codes. If transferring a substance to a secondary container (like a squeeze bottle or smaller jar), one must replicate essential information: name of the chemical, hazard warnings, relevant pictogram, or at least a simplified label if the chemical is used immediately. Failing to label secondary containers raises the risk of mix-ups or unsuspecting exposure, so consistent labeling forms a cornerstone of safe practice.
3.2. Workplace Label Systems
Some workplaces adopt color-coded or alphanumeric label systems that convey details about flammability, reactivity, and personal protection. NFPA diamond or the HMIS (Hazardous Materials Identification System) approach might be used in the United States. If chemicals are stored for extended periods, periodic inspection ensures labels remain legible, and chemicals are not degraded or mislabeled. For instance, older containers might have damaged or missing labels, prompting proper re-labeling or disposal.
4. Storage and Segregation
4.1. Segregation by Compatibility
Certain chemicals react dangerously if they come into contact, so grouping them by hazard class helps avoid accidental spills or cross-contamination. For instance:
- Flammables: Store in designated flammable cabinets, away from ignition sources.
- Oxidizers: Keep separate from fuels or reducing agents, as they can spark violent reactions.
- Acids: Separate from bases to avoid exothermic neutralization or harmful fumes.
- Poisons and Toxics: Lock in secure cabinets with restricted access.
Dedicated cabinets or shelves with chemical-resistant surfaces and ventilation lower the risk of reactions. Spacers or secondary containment trays can catch leaks. Some labs maintain refrigerators specifically for volatile chemicals at low temperatures, ensuring that these units have no internal sparks or other ignition sources.
4.2. Temperature and Ventilation
Storing chemicals under recommended conditions helps preserve stability. Light-sensitive substances might degrade under strong illumination, so amber glass or opaque wrapping is used. Others degrade at high temperatures, so they may need refrigeration. Corrosive vapors demand well-ventilated enclosures or specialized acid cabinets with coated metal components. In highly flammable settings, ensuring no open heating elements or electrical arcs is essential. When dealing with cryogens (e.g., liquid nitrogen), one must ensure spaces have adequate oxygen sensors or ventilation to prevent asphyxiation hazards.
5. Personal Protective Equipment (PPE)
5.1. Basics of PPE
Equipment worn to shield individuals from chemical contact includes gloves, goggles, face shields, lab coats, aprons, and respirators. The specific choice depends on the hazards:
- Gloves: Must resist permeation by chemicals in use. Latex or vinyl might suffice for mild tasks, but nitrile or neoprene can block solvents or corrosives.
- Eye/Face Protection: Safety glasses with side shields protect from splashes. Goggles or face shields are mandatory when working with highly corrosive or reactive solutions.
- Clothing: A flame-resistant (FR) lab coat shields from small fires or chemical splashes. Sturdy, closed-toe shoes keep spills off feet.
- Respirators: Required for airborne threats (dust, fumes, vapors). Cartridge or air-supplied respirators chosen based on the type of contaminant and permissible exposure limits.
Training ensures proper fit and maintenance. Gloves can degrade over time, so frequent inspection is vital. People sometimes choose gloves hastily, risking chemical penetration if incompatible materials are used.
5.2. Safe Use and Limitations
PPE forms the last defense layer. Administrative controls (like reducing volumes or using alternative methods) often better reduce hazard potential. Over-reliance on PPE can breed complacency if other safety measures are inadequate. Also, certain gear can limit dexterity or obscure vision, affecting comfort and performance. Balancing protective benefits with practicality helps maintain consistent compliance. Replacing worn or torn equipment promptly ensures continued efficacy.
6. Safe Handling Techniques
6.1. Basic Precautions
When handling chemicals, never eat, drink, or apply cosmetics in the workspace. Wash hands after removing gloves, even if no apparent spill occurred, as microscopic residues might remain. Keep surfaces clean and uncluttered, storing chemicals away from direct bench space unless immediately used. Always read the SDS or label prior to opening new substances, especially if unfamiliar. Check for signs of container damage, unusual precipitates, or discoloration that might signal contamination or decomposition.
6.2. Using Fume Hoods
For volatile or hazardous fumes, a fume hood provides local ventilation, preventing toxic inhalation. Users should position equipment and chemicals at least six inches behind the sash, adjust the sash at recommended working height, and minimize sudden movements that disturb airflow. Regular testing ensures hoods maintain adequate face velocity. Alarms or monitoring devices alert staff if airflow drops below safe levels. Note that fume hoods are not for chemical storage unless specifically designed with extra ventilation or dedicated cabinetry.
6.3. Transfer and Measurement
Transferring chemicals typically involves weigh boats, spatulas, pipettes, or funnels. One should avoid direct skin contact by wearing gloves, and ensure containers remain closed unless in active use. If a product is highly reactive or air/moisture sensitive (e.g., alkali metals, strong organometallic reagents), inert atmosphere techniques with glove boxes or Schlenk lines help keep out oxygen or humidity. For flammable solvents, static discharge can spark fires, so grounding containers and using spark-free equipment or ventilation can reduce ignition risks.
7. Emergency Preparedness
7.1. Spill Response
Even well-managed areas can encounter spills. Swift containment is key:
- Alert People: Clear the area, announce the spill, and assess the hazard level (small vs. large, flammable vs. toxic).
- PPE and Supplies: Don suitable gloves, goggles, or respirators. Use spill kits with absorbents (e.g., universal pads, neutralizers, or special materials for mercury).
- Contain and Clean: Block drains to prevent runoff. Soak up or neutralize residues. Place waste materials in sealed containers labeled as hazardous.
- Ventilation: Enhance airflow if fumes are present.
- Report and Document: Adhere to local procedures, contact safety officers if the incident is large or complicated.
Large spills involving extremely toxic or explosive chemicals may exceed personal cleanup capacity, requiring specialized HAZMAT teams.
7.2. Fire Safety
Laboratories and storage areas must have fire extinguishers rated for flammable liquids (class B) or for various hazards. Staff should learn how to use extinguishers (Pull, Aim, Squeeze, Sweep method) but also know when evacuation is safer. Sprinkler systems, fire doors, and alarm pull stations help contain and control fires. Minimizing flammable inventories, sealing containers properly, and ensuring no unprotected ignition sources exist near flammable vapors also reduce fire risk. In certain advanced labs, inert gas systems can displace oxygen if a fire starts.
7.3. First Aid and Decontamination
If skin contact occurs with corrosives, rinse thoroughly under running water for 15 minutes, removing contaminated clothing or jewelry. For eye splashes, use eyewash stations, forcibly holding eyelids open. Inhalation incidents require moving the individual to fresh air. Burns from chemicals or thermal sources might need immediate cooling before further evaluation. Everyone in the workspace should be trained in basic first aid, while specialized rescue or medical staff handle severe cases. Documenting each incident, even if minor, can help refine protocols and prevent repeat scenarios.
8. Waste Management and Disposal
8.1. Hazardous Waste Classification
A chemical waste often qualifies as hazardous if it’s flammable, corrosive, reactive, or toxic. Regulatory frameworks (like the Resource Conservation and Recovery Act in the U.S.) mandate that such wastes be stored, transported, and disposed of via permitted facilities. The generator must identify chemical constituents, label containers, and keep them closed unless actively adding waste. Mixing incompatible wastes (e.g., oxidizers with flammables) can provoke violent reactions, so thorough segregation remains essential.
8.2. Minimizing and Recycling
Waste reduction strategies include using micro-scale reactions, substituting less dangerous chemicals, and implementing solvent recycling. For instance, distillation units can purify used solvents, cutting disposal volumes. Using water-based cleaning solutions instead of organic solvents also helps. In some cases, nonhazardous byproducts can be neutralized or evaporated with minimal risk, but only if local regulations permit. The concept of “green chemistry” supports these principles, advocating design of procedures that prevent pollution at the source.
9. Training and Culture
9.1. Orientation and Ongoing Instruction
New employees or students working with chemicals should complete hazard communication training, learn about PPE requirements, and review standard operating procedures for tasks they will undertake. Hands-on demonstrations, real scenario exercises, and checklists reinforce theoretical knowledge. Periodic refresher sessions keep staff updated on changes in regulations, new chemicals, or revised protocols. Management must provide resources for continuous learning, including accessible SDS repositories and signage around the facility.
9.2. Fostering Shared Responsibility
Chemical safety is a team effort. Supervisors, EHS (environmental health and safety) personnel, and staff members coordinate on risk assessments, audits, and improvement strategies. Peer observation and feedback can catch unsafe habits early. Incident reporting systems allow people to submit concerns or near misses without fear of blame. This culture of open communication fosters mutual responsibility, ensuring that everyone has a stake in maintaining a safe environment. Recognition of positive safety behaviors, transparency about incidents, and consistent policy enforcement underscore that safe conduct is a core value.
10. Legislation and Standards
10.1. Regional Regulatory Bodies
Various jurisdictions impose rules on chemical handling, worker safety, and environmental discharge. Examples include:
- OSHA in the U.S. sets workplace exposure limits, known as Permissible Exposure Limits (PELs), and mandates hazard communication.
- European Chemicals Agency (ECHA) enforces REACH (Registration, Evaluation, Authorization, and Restriction of Chemicals) to protect health and the environment from chemical risks.
- Health and Safety Executive (HSE) in the UK handles oversight of chemical usage and hazard management.
Businesses operating internationally must align with multiple frameworks, each with specific labeling, packaging, and recordkeeping obligations.
10.2. Voluntary Guidelines
Professional organizations (e.g., American Chemical Society, Royal Society of Chemistry) publish best practice guides for safe laboratory operations. Universities often adopt these guidelines for academic labs, complementing mandated rules. Accredited standards (like ISO 45001 for occupational health and safety) can also shape organizational policies, establishing systematic approaches to hazard identification, staff training, and risk control.
11. Working with Particularly Hazardous Substances
11.1. Carcinogens, Teratogens, and Reproductive Toxins
Some chemicals raise serious health concerns if inhaled or absorbed over time. Substances listed as “select carcinogens” require restricted access, specialized ventilation, and rigorous PPE. Work with such toxins might occur within designated areas labeled “Carcinogen Use Area,” demanding advanced training. Employers must monitor airborne concentrations and track potential exposures. Regular medical surveillance may be advised for people handling them frequently.
11.2. High Reactivity and Explosives
Compounds that can detonate under shock, heat, or friction necessitate protective barriers and minimal handling quantities. Picric acid, peroxides, or nitrated materials might degrade into highly unstable forms if stored improperly. Peroxide-forming solvents (ether, tetrahydrofuran) can accumulate explosive crystals over time, so dating containers and testing for peroxides is essential. Facilities sometimes rely on automation or remote handling for extremely sensitive substances.
11.3. Biological and Radioactive Hazards
Though not purely chemical, these also introduce safety concerns. Biohazards might involve infectious microorganisms, requiring biosafety cabinets and sterilization procedures. Radioactive isotopes require shielding, specialized storage, and strict licensing. Combining chemical toxicity with radiological or biological risks intensifies the complexity of safe handling. Labs dealing with such materials often enforce additional training, elaborate documentation, and monitoring programs for contamination or dose levels.
12. Final Synopsis
Chemical safety is a shared responsibility. Organizations must identify and label hazards, store and segregate substances properly, train staff to handle materials, and prepare for emergencies. Individuals need to wear appropriate PPE, respect signage, and remain vigilant for potential issues such as worn gloves, unlabeled containers, or suspicious odors. Good recordkeeping and consistent housekeeping reduce accident chances, while conscious decision-making about waste minimization supports environmental protection.
As industries evolve, new compounds and processes appear, leading to fresh concerns about toxicity or reactivity. Regulations adapt, adding clarity to hazard communication. Workers who understand the principles behind safe chemical handling foster a culture of prevention and well-being, making labs, factories, and classrooms places of innovation without sacrificing health or ecological balance.